摘要: 原料的反应特性、反应器入口分配效果、催化剂体系及其级配技术会影响RHT渣油加氢装置的高效运行。原料的反应特性影响催化剂的杂原子脱除率和残炭前身物加氢转化性能,还会影响催化剂的失活机制和装置运转周期;反应器入口分配效果不佳会导致较高的床层径向温差;催化剂级配不合理会影响整体催化剂的活性和稳定性;渣油的分子大、黏度高,在催化剂中传质阻力大,扩散速度慢。针对这些影响RHT装置高效运行的主要因素,中国石化石油化工科学研究院结合基础研究和应用研究的结果,开发了相应的RHT系列技术,包括量体裁衣的RHT催化剂及级配技术、原油脱钙技术、反应器物流高效分配技术、可切除和可轮换的保护反应器工艺以及RICP系列工艺。根据RHT装置加工原料的特点以及全厂总流程的安排,针对不同的RHT装置提出了不同的整体解决方案。3套RHT装置的工业应用结果表明,实施整体解决方案后,RHT装置均实现了高效运行。
关键词: RHT固定床渣油加氢 高效运行 整体解决方案
固定床渣油加氢的主要用途是给催化裂化装置提供原料,也是生产低硫重质船用燃料油的主力装置。渣油加氢的主要目标为脱除金属、硫、氮等杂质、实现残炭前身物加氢转化和提高氢含量,有助于降低催化裂化剂耗和增加催化裂化装置轻油收率,从而实现石油资源的清洁、高效利用【1-2】。从1994年以来,中国石化石油化工科学研究院(简称石科院)致力于渣油加氢催化剂及相关工艺技术的开发,RHT固定床渣油加氢催化剂及级配技术于2002年首次实现工业应用,2006年RHT工艺及RICP工艺也首次实现工业应用。截止到目前,采用RHT技术建成投产的渣油加氢装置有6套,在建的RHT渣油加氢装置有3套。石科院考察了影响渣油加氢高效运行的因素,发现加工不同反应特性的原料需要相适应的催化剂和级配技术,加氢处理高铁和高钙含量渣油时保护反应器压降会快速升高,渣油的黏度较大,会影响反应器的物流分配和加氢反应效果,渣油加氢催化剂失活的原因与馏分油加氢催化剂明显不同等,并针对这些问题持续升级原有技术,研究并开发出相应的新技术,为RHT装置高效运行提供整体解决方案。
1、RHT系列技术的开发
1.1 RHT催化剂和级配技术
1.1.1 RHT系列催化剂
渣油加氢催化剂主要分为保护剂和主催化剂,其中主催化剂分为脱金属剂、脱金属脱硫剂、脱硫脱氮或脱硫降残炭剂。石科院针对渣油原料中含有一些25 μm规格的反冲洗过滤器也无法过滤掉的微小铁垢(没有滤掉的这部分杂质会分散到反应器下游),开发了容垢能力更强的泡沫状保护剂,可以容纳更多的颗粒垢物和无机铁。在主催化剂方面,通过优化金属活性相结构来提高催化剂的活性位数量;通过改进活性金属负载工艺,使活性组分分散良好,提高了催化剂的本征活性;通过载体表面性质改性,减少运行时催化剂的表面积炭量,开发了适宜沥青质和反应双通道孔分布的脱金属催化剂、活性缓慢释放的脱金属脱硫剂以及提高催化剂的有效反应表面和活性中心的可接近性的加氢脱硫降残炭剂。
1.1.2 RHT催化剂级配
催化剂级配在渣油加氢反应过程中起着非常重要的作用。研究表明,渣油加氢催化剂失活的主要原因是积炭和金属沉积[3]。一般而言,馏分油加氢催化剂主要因结焦而失活,在加工高硫渣油原料时,其金属(Ni+V)含量较高,渣油加氢催化剂失活的主要原因是金属Ni和V的硫化物沉积。如果脱硫剂比例过高,虽然催化剂的整体初期活性高,但是容金属Ni和V能力较低,使催化剂寿命缩短;如果脱金属剂比例过高,容金属Ni和V的能力提高,但是催化剂整体活性会降低。此外不同类型渣油原料反应特性不同,表1为在相同的工艺条件和催化剂级配下,两种原料的加氢试验结果[4-5]。由表1可见,相对于高硫渣油,低硫渣油的杂原子脱除率和降残炭率均明显较低,表明不同类型的原料具有不同的反应特性。
表1 两种渣油原料及其加氢生成油的主要性质
基于对原料反应特性和催化剂性能的认识以及构建的反应动力学和催化剂失活模型,结合上述新的RHT系列催化剂,石科院开发了为炼油企业“量体裁衣”的催化剂级配技术。
1.2 原油脱钙技术
一些原油钙含量较高,绝大部分分布于渣油中,渣油中的有机钙化合物会在加氢条件下发生加氢脱钙反应生成CaS,且以结晶的形式沉积在加氢催化剂(保护剂)颗粒外表面[3,5],使得催化剂床层的空隙率降低,从而引起反应器压降增加、催化剂利用率降低[6]。某炼油厂曾加工未经脱钙处理的高钙原油,常减压蒸馏装置所得的渣油馏分进入固定床渣油加氢装置进行加氢处理。图1为该炼油厂渣油加氢装置A、B两列第一反应器(一反,R-101)压降的变化情况[7]。由图1可以看出,装置仅运转100 d,其A、B两列的一反压降就开始上升,运转230 d后一反压降高于0.5 MPa,严重影响装置的正常运行。
图1 某炼油厂渣油加氢装置一反压降变化情况
▲—A列一反;●—B列一反
董凯等[6]的研究结果表明,含钙化合物可以分为易脱除含钙化合物和难脱除含钙化合物,胶质中的含钙化合物容易脱除,通过原油脱钙剂即可脱除,原油经脱钙后,渣油中的含钙化合物主要分布于沥青质中,且几乎全部为难脱除含钙化合物,较难转化为CaS,对渣油加氢装置的影响大幅降低。基于该基础研究,石科院开发了针对高钙原油的脱钙技术,其工艺流程示意如图2所示。原油经脱钙处理后,常减压蒸馏装置所得的渣油再引入RHT装置进行加氢处理。
图2 针对高钙含量原油的脱钙技术工艺流程示意
1.3 反应器物流高效分配技术
由于渣油原料黏度较大,物流在反应器内的分配均匀非常重要。物流分配是否均匀直接影响加氢反应效果和装置的长周期运行。研究表明,渣油加氢物流分配不均匀容易导致催化剂床层热点的产生,并且热点往往出现在液速较低的局部区域[8]。由于液速低,油品发生深度转化(如发生强放热的热裂化等反应),导致该区域出现热点。
基于对渣油原料性质和工程流体力学的深入认识,石科院开发了渣油加氢反应物流高效分配技术[5]。某炼油厂渣油加氢装置采用石科院新型分配器后的使用情况见表2。由表2可以看出,采用石科院新型分配器时,原料中减压渣油掺炼比例较采用常规分配器时高,原料的性质变差,但仍然能够显著降低各反应器最大径向温差。
表2 常规分配器和新型分配器使用情况对比
1.4 可切除和可轮换的保护反应器工艺
一些炼油厂渣油的铁含量较高,其中油溶性的含铁化合物在加氢条件下转化为FeS,并沉积在催化剂颗粒间或呈“蛋壳状”分布在催化剂表面[3,5,9],催化剂床层的空隙率降低,导致反应器压降增加和催化剂利用率降低。为进一步延长装置运转周期,对于铁含量高的渣油,石科院开发了保护反应器可切除的工艺[5],工艺流程示意如图3所示。在保护反应器压降升高到限定值时,采用该工艺技术可延长渣油加氢装置的运转周期。
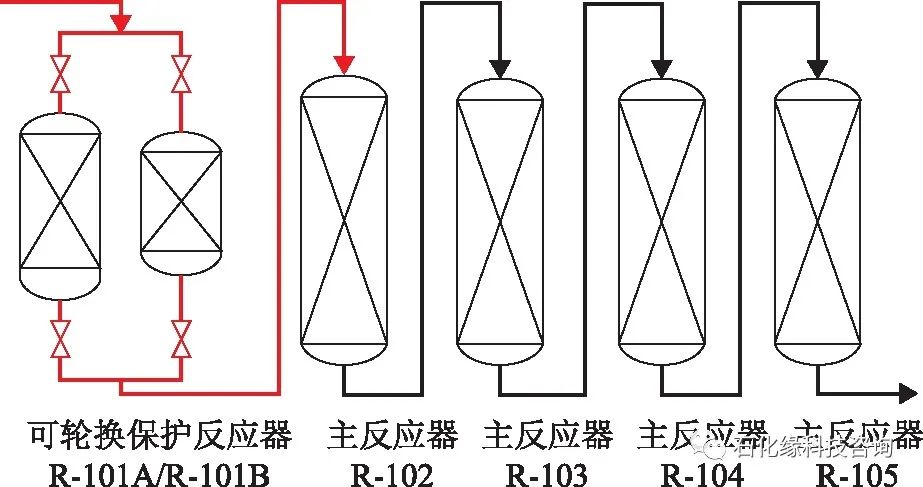
图3 保护反应器可切除工艺的流程示意
针对金属(Ni+V)质量分数为150~200 μg/g的渣油原料,石科院开发了可轮换的保护反应器工艺,工艺流程示意如图4所示[5,10]。该工艺采用两个可轮换的保护反应器,当其中一个保护反应器不能运转后,将反应物流引入到另一个保护反应器中,并置换切除的保护反应器中的催化剂,再经硫化后等待下一次轮换(或直接置换硫化态的催化剂)。该技术已完成工艺开发,运转周期可以达到2~3年。
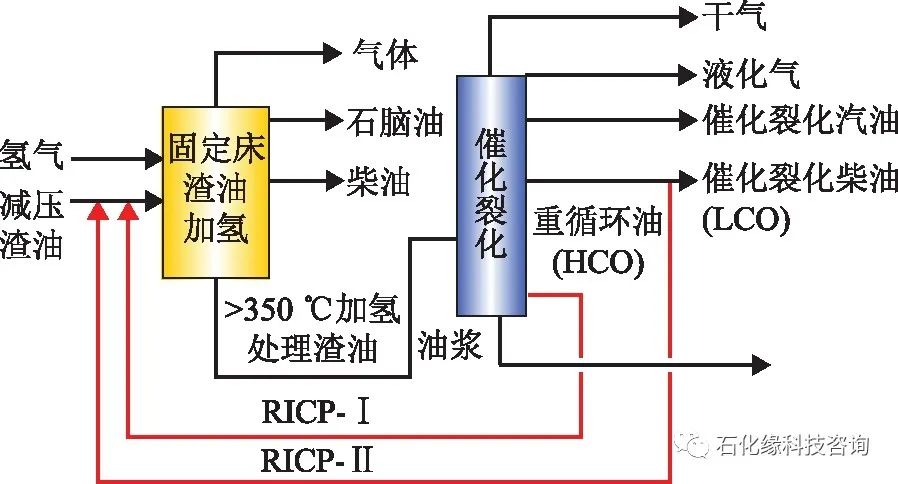
图4 可轮换保护反应器工艺的流程示意
1.5 RICP系列工艺
一般而言,渣油加氢过程中反应物流与催化剂充分接触,反应物分子需扩散进入到催化剂孔的内表面才能发生加氢反应,因此内扩散常常是渣油加氢过程的控制步骤[11]。渣油的黏度与分子大小是影响渣油加氢反应的2个重要参数。采用石科院开发的RICP系列工艺可以降低渣油加氢原料的黏度,促进渣油加氢脱除硫、金属和沥青质等杂质的反应及残炭前身物加氢转化反应的进行[9-12]。RICP系列工艺的流程示意如图5所示。
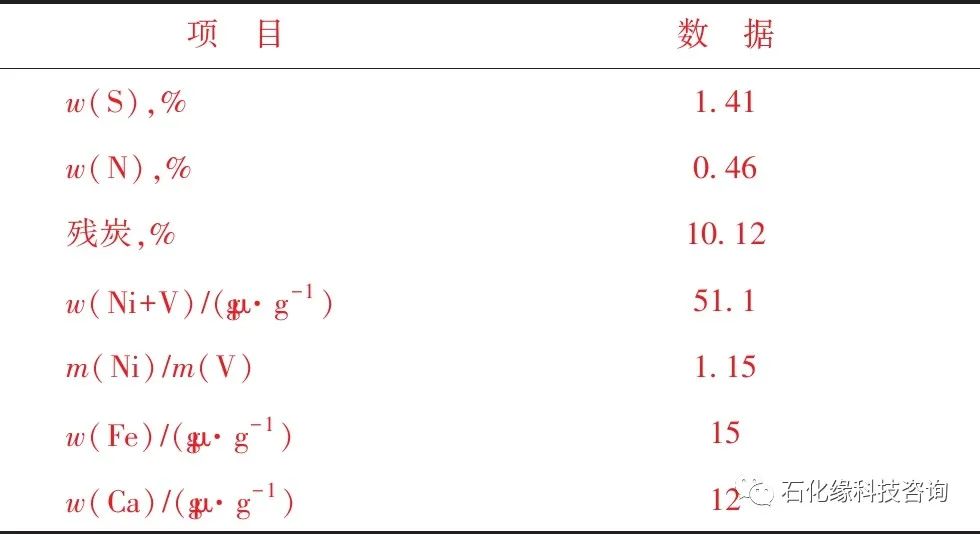
图5 RICP系列工艺的流程示意
2、RHT系列技术的应用
在已开工的RHT装置中,石科院根据加工原料的特点以及全厂总流程的安排,针对不同的RHT装置提出了相应的整体解决方案,实现了RHT装置的高效运行。
2.1 某2.0 Mta RHT装置
2.1.1 装置原料性质
该炼油厂加工高钙原油,实施了原油脱钙技术,装置的典型原料性质见表3。由表3可以看出,该装置的原料特点为:硫含量低、氮含量较高、残炭适中、金属(Ni+V)含量适中(其中Ni含量高、V含量低)、铁含量较高。
表3 某2.0 Mt/a RHT装置的原料性质
2.1.2 装置解决方案及运行效果
根据该厂原油及RHT装置的原料特点,采用了以下RHT系列技术:①相适应的RHT系列催化剂及级配技术;②原油脱钙;③可切除的保护反应器;④RICP-Ⅰ工艺。
该装置第三运行周期(简称RUN-3)中保护反应器(R-101)的压降、各反应器平均温度及装置所有催化剂平均反应温度(CAT)、原料和加氢常压渣油(简称加氢常渣)残炭随运转时间的变化情况分别见图6~图8。
由图6可见,装置的运转周期一共达到了535 d,其中保护反应器压降在运行473 d后达到了限定值0.7 MPa,保护反应器切除后,装置继续运行了62 d。
保护反应器切出前,其床层温升相当低,说明该反应器中催化剂已基本失去活性。保护反应器切出后,体积空速增加,但提高R-102,R-103,R-104的反应温度(见图7)后,催化剂的降残炭率基本没有变化(见图8),切除保护反应器后,加氢常渣的残炭均低于5.5%(控制指标),依然是较好的催化裂化装置原料,表明保护反应器可切除的工艺可行,不仅装置的运行周期延长,催化剂的活性也得到充分发挥。同时切除保护反应器后,催化剂的残炭前身物加氢转化性能优良,说明RHT系列催化剂的级配技术合理。

图6 保护反应器R-101压降随运转时间的变化
图7 反应器平均反应温度随运转时间的变化
—R-101; —R-102; —R-103;
—R-104; —R-105;●—CAT
图8 原料和加氢常渣残炭随运转时间的变化
◆—原料;●—加氢常渣
RICP-Ⅰ工艺投用前后催化裂化装置的标定结果见表4。由表4可见,RICP工艺实施后,催化裂化装置新鲜进料量增加16.72 t/h,液化气收率增加2.51百分点、汽油收率增加0.91百分点,总的液体收率增加3.30百分点,提高了高价值产品的产量。
表4 RICP-Ⅰ实施前后催化裂化装置的标定结果
1)RICP投用后减去RICP投用前的差值。
2.2 某1.7 Mt/a RHT装置
2.2.1 装置原料性质 某炼油厂加工高钙原油,同样实施了原油脱钙技术,其1.7 Mt/a RHT装置的典型原料性质见表5。由表5可见,该装置的原料特点为:硫含量低、氮含量高、残炭适中、金属(Ni+V)含量适中(其中Ni含量高、V含量低)、铁含量较高。
表5 某1.7 Mt/a RHT装置的原料性质
2.2.2 装置解决方案及运行效果
根据该厂加工原油及RHT装置原料特点,采用了以下的RHT系列技术:①不断提升的RHT系列催化剂及级配技术;②原油脱钙技术;③高效分配技术;④RICP-Ⅱ 工艺。
由于该装置没有采用保护反应器可切除的技术,因此催化剂及级配技术持续改进和提升,第一运行周期(简称RUN-1)和第二运行周期(简称RUN-2)中R-101压降随铁、钙沉积量(以R-101催化剂体积计)的变化如图9所示。由图9可见,R-101压降达到限定值(0.70 MPa)时,RUN-1中铁和钙的沉积量为0.0185 6 t/m3,RUN-2中铁和钙的沉积量为0.212 5 t/m3,增加了铁和钙的沉积容量,有利于延长装置的运转周期。
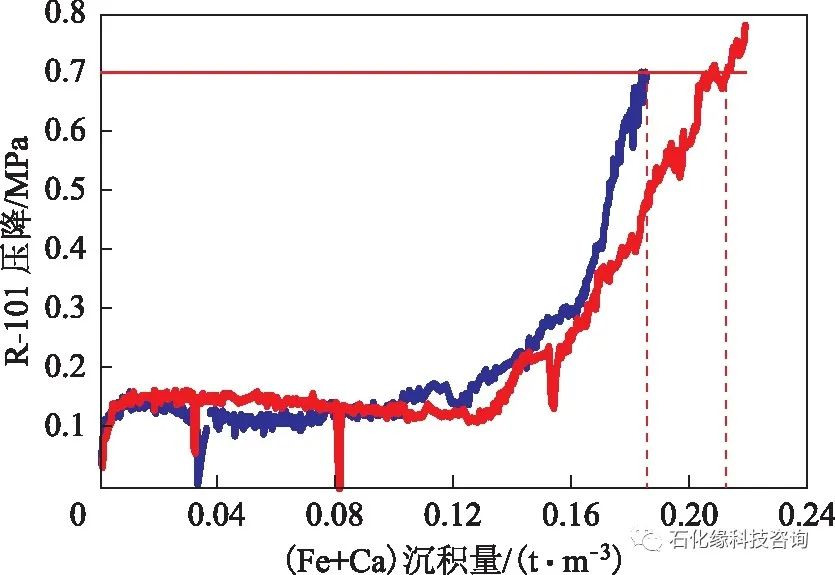
图9 R-101压降随Fe和Ca在R-101沉积量的变化
—RUN-1; —RUN-2
RUN-2中,在R-101反应器中应用了RHT物流高效分配器。图10为该装置在RUN-1和RUN-2两个周期中R-101最大径向温差随运转时间的变化情况。由图10可见,采用高效分配器后,R-101最大径向温差大幅降低,有利于催化剂整体活性的发挥[5,9,13]。
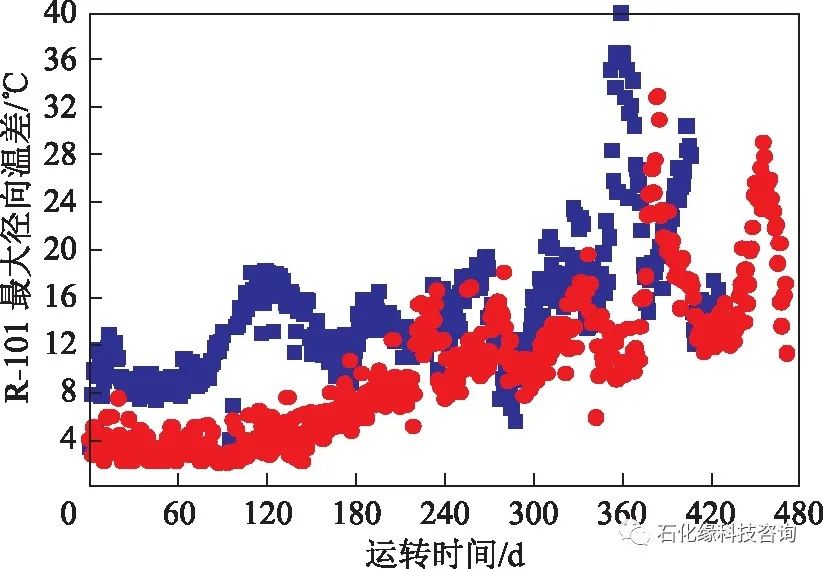
图10 R-101最大径向温差随运转时间的变化
■—RUN-1;●—RUN-2
该装置原料氮含量较高,会增加催化剂上的积炭量,而RICP技术可抑制催化剂上炭的生成[1-2]。基于RICP的理论认识,装置在第四运行周期(RUN-4)实施了RICP-Ⅱ技术,同时原料性质也进行了适度优化,RUN-4实现了693 d的超长周期运转[14]。RUN-2和RUN-4两个周期中的CAT、R-101压降和降残炭率随运转时间的变化如图11~图13所示。由图11~图13可见,与RUN-2相比,RUN-4的反应温度低,R-101压降上升速度慢,降残炭率提高。
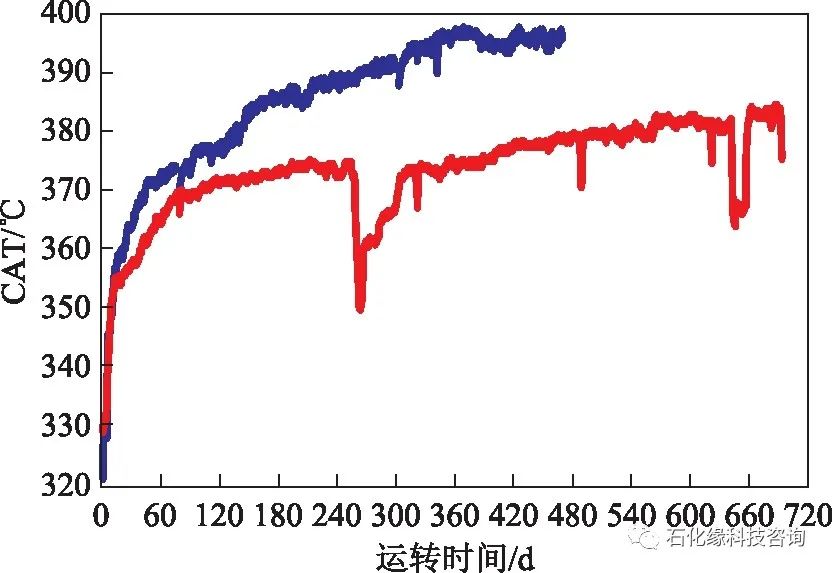
图11 CAT随运转时间的变化
—RUN-2; —RUN-4。图12同
图12 R-101压降随运转时间的变化
图13 降残炭率随运转时间的变化
■—RUN-2;●—RUN-4
2.3 某3.9 Mt/a RHT装置
2.3.1 装置原料性质
某3.9 Mt/a RHT装置典型原料性质及特点见表6。由表6可以看出,该装置所加工原料的特点为:硫含量高、氮含量低、残炭高、金属(Ni+V)含量高(其中Ni含量低、V含量高)、铁和钙含量低。
表6 某3.9 Mt/a RHT装置的原料性质
2.3.2 装置解决方案及运行效果
根据该厂加工原油及RHT装置原料特点,采用了以下的RHT系列技术:①相适应的RHT系列催化剂及级配技术;②RICP-Ⅱ工艺。
在RUN-1中装置的进料量随运转时间的变化如图14所示。由图14可见,运转60 d后装置的实际进料量高于设计进料量,装置长期处于高负荷运转,共运行了582 d。RUN-1中原料和加氢常渣硫含量、残炭和金属(Ni+V)含量随运转时间的变化如图15~图17所示。由图15~图17可见,该装置运转稳定,加氢常渣硫含量、残炭和金属(Ni+V)含量均满足催化裂化原料的指标要求,实现了装置的高效运转。
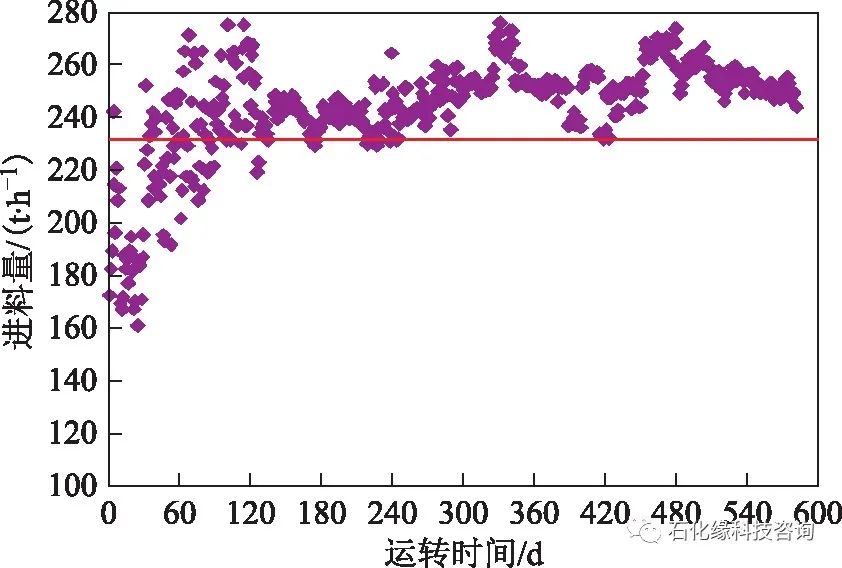
图14 进料量随运转时间的变化
◆—实际进料量; — 设计进料量
图15 原料和加氢常渣硫含量随运转时间的变化
◆—原料;●—加氢常渣
图16 原料和加氢常渣残炭随运转时间的变化
◆—原料;●—加氢常渣
图17 原料和加氢常渣金属(Ni+V)含量随运转时间的变化
◆—原料;●—加氢常渣
3、结 论
(1)石科院开发了RHT系列技术:先进的催化剂及量体裁衣的催化剂级配技术,是更高产品质量及更长运转周期的保障;原油脱钙技术的开发拓展了渣油加氢装置的原料品种,为炼油厂选择低价原油提供了支撑;高效分配技术改善了反应器内的物料分布,充分发挥所有催化剂的作用,消除影响渣油加氢长周期运转的隐患;可切除和可轮换保护反应器技术的开发,为炼油厂加工高金属含量的原料提供了技术选择;RICP系列技术的开发实现了渣油加氢与催化裂化的高效组合,改善了渣油加氢的反应性能,增加了高价值产品的收率。
(2)根据原料及装置的特点、全厂总流程安排,RHT系列技术可以为RHT装置提供高效运行的总体解决方案;工业应用案例表明,总体解决方案在提升产品品质的同时可有效延长RHT装置的运转周期,改善企业经济效益,提高石油资源的有效利用率。
作者:邵志才,刘 涛,邓中活,胡大为,沈明欢,王少兵,戴立顺,杨清河( 中国石化石油化工科学研究院 )